The 6-Step Guide To Maintaining Safety Data Sheets (SDS) For Workplace Safety
- Published On:
- (SDS) / Chemical Management, App Builder
Every year, chemical exposures in the workplace lead to accidents. Around 50,000 workers die each year in the US due to workplace injuries. Safety Data Sheets (SDS) are key to preventing these incidents, they provide crucial information about chemical hazards. Without them, we’re walking in the dark.
Safety data sheets are a must-have for workplace safety. OSHA requires them through the Hazard Communication Standard. A good SDS system keeps everyone safe, It lowers risks and boosts your safety culture. This guide breaks it down into six simple steps. You can achieve a safer, compliant workplace by following these steps.
Step 1: Understanding SDS Requirements and Your Responsibilities
SDS aren’t just suggestions. They’re the law. You must know your duties to stay compliant. Both employers and employees have roles to play here. What are your responsibilities?
Deciphering OSHA's Hazard Communication Standard (HCS)
The Hazard Communication Standard (HCS) is OSHA’s rule book for chemical safety. It ensures employers and employees know about chemical hazards and how to protect themselves.
SDS accessibility is a core piece of HCS. Employees must know where to find SDS.
They should also know how to use the information.
- Access OSHA Resources: Keep these on hand. Access OSHA’s Hazard Communication page for details. Also, read interpretations of the HCS.
- Training is Key: Make sure your employees know about SDS.
- Stay Updated: Rules can change, so always know the latest updates.
Identifying Your SDS-Related Duties as an Employer
As an employer, the weight is on your shoulders. You must get and keep SDS for every hazardous chemical in your workplace. These sheets must always be easy to access. Also, your employees must understand them through training. Not following these rules can lead to big problems. Also, accidents can happen. Imagine a worker using a chemical without knowing its dangers.
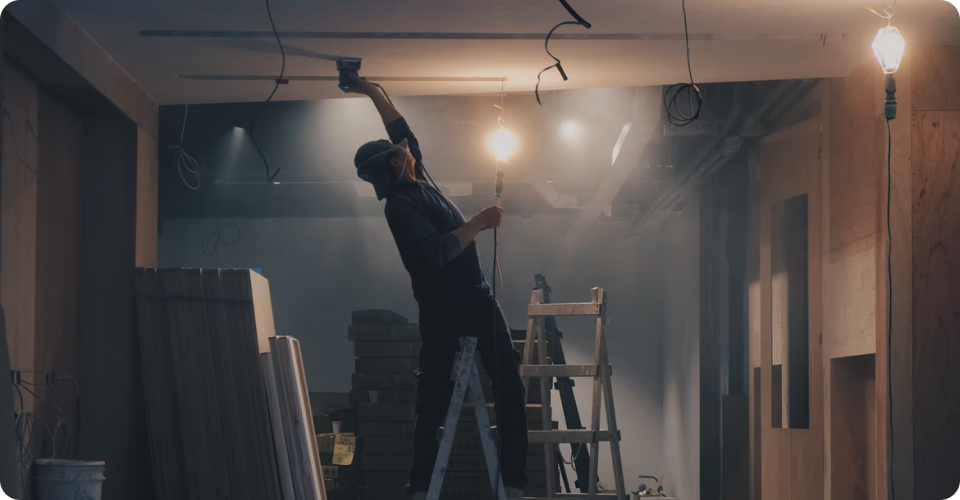
Step 2: Compiling and Organizing Your SDS Collection
Getting all your SDS together is the next move. You need to request them from manufacturers and suppliers. Then, set up a system to keep them organized. A disorganized system is as good as no system at all. How do you keep track of dozens, or even hundreds, of these sheets?
Establishing a System for Obtaining SDS
Start by asking your suppliers for SDS. Blanket requests are a great way to get all the SDS you need. Also, check if your suppliers have online portals. These often have SDS available for download.
- Create a Template: A standard email for requesting SDS can save time. Be polite, but firm.
- Blanket Requests: Ask all your suppliers for SDS, for every chemical.
- Online Portals: Many suppliers have SDS online. Check these out too.
Implementing a Logical Filing and Indexing System
How you organize your SDS matters. Pick a system that works for you and your team. Alphabetical order is a common choice. You could also organize by department or by hazard type. No matter what you choose, make sure it is easy to find what you need. Cross-referencing is key too. This means linking different SDS together.
Think of your SDS collection like a library. You want to be able to find what you need, fast.
Step 3: Ensuring SDS Accessibility for All Employees
SDS are useless if workers can’t access them. Make them easy to find in all work areas. This means both paper and electronic copies. Make sure everyone knows where they are.
Multiple Access Points: Paper and Electronic
SaPaper SDS are good for quick reference, but they can get lost or damaged. Electronic SDS are easy to update and share. However, workers need computers to see them. A mix of both is often the best way to go.
- Paper Copies: Keep printed SDS in binders in central locations.
- Electronic Access: Store SDS on a shared drive or use Safety data sheet management software.
- QR Codes: Put QR codes on chemical containers. Link these to the online SDS.
Training Employees on How to Locate and Interpret SDS
Just having SDS isn’t enough. Employees must know how to find and read them. Train them on both the paper and electronic systems. Make sure they understand the information in the SDS. This is how they can protect themselves from chemical hazards.
How can you ensure your team understands SDS? Regular training is essential.
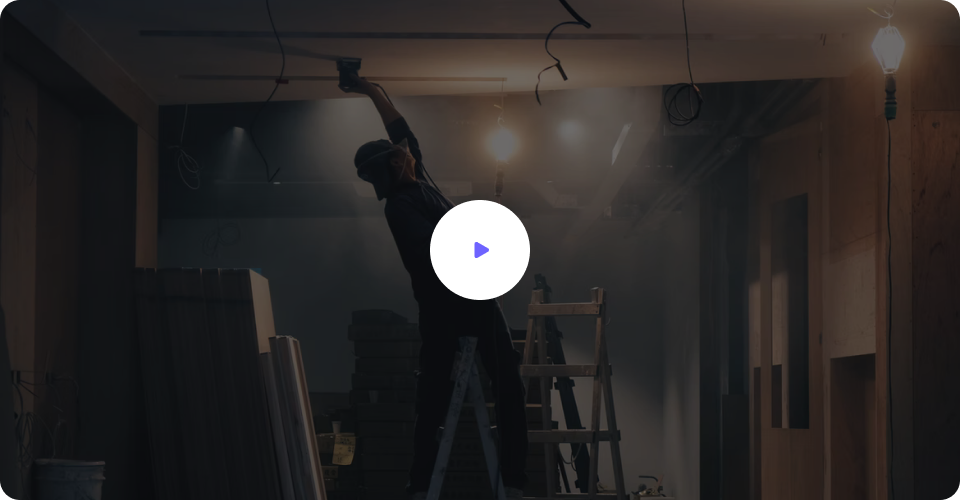
Step 4: Regularly Updating and Reviewing Your SDS Inventory
Chemicals and regulations change. SDS must be up-to-date. Review your SDS regularly and replace any that are old.
Establishing a Schedule for SDS Review
Set a schedule to check your SDS. Once a year is a good start. But, you should also review SDS when you get a new chemical. Or, if you learn about new hazards. Set reminders to keep on track.
- Annual Review: Check all SDS once a year.
- New Chemicals: Review SDS when you bring in new chemicals.
- Calendar Reminders: Use your calendar to remind you to review your SDS.
Tracking and Replacing Outdated SDS
How do you know if an SDS is outdated? Check the revision date. If it’s more than a few years old, get a new one. Contact your suppliers for updated SDS. Also, you can search online databases.
Outdated SDS are as dangerous as no SDS at all.
Step 5: Training Employees on SDS Content and Safe Handling Practices
Now, dig into the SDS content. Teach your employees what the sections mean. Show them how to use the information to work safely.
Translating SDS Information into Practical Safety Procedures
SDS information is only helpful if it changes how people work. Use SDS to create safe work rules. Pick the right PPE. Also, plan for emergencies.
Example: An SDS says a chemical causes skin burns. The safety rule should require gloves and eye protection when working with the chemical. A spill plan should be in place, and a way to rinse skin in the event of a burn.
Step 5: Training Employees on SDS Content and Safe Handling Practices
Keep records of your SDS management. This shows you’re following the rules. It also helps you improve your system over time.
Record-Keeping Best Practices for SDS Management
What records should you keep? Keep copies of all SDS. Also, keep training records. And, keep records of your SDS reviews. Store these records for as long as OSHA requires. This depends on the type of record.
- SDS Copies: Keep all SDS, even old ones.
- Training Records: Track who was trained and when.
- Audit Reports: Record your SDS reviews.
- Retention: Know how long to keep each type of record.
Preparing for OSHA Inspections Related to SDS
OSHA may visit your workplace. Be ready for an inspection. Have your SDS ready to show them. Also, show them your training records. A good SDS system can make inspections go smoothly.
Do you have these ready for an OSHA inspector?
- SDS readily available.
- Employee training records.
- A written hazard communication program.
Conclusion
Maintaining SDS compliance doesn’t have to be a headache. Knowella simplifies the process. Knowella’s enterprise-grade SaaS platform empowers companies to build no-code apps for efficient operations, safety, quality, and compliance management.
Knowella helps businesses automate complex workflows, reduce human errors, and improve compliance tracking. Its intuitive dashboard provides real-time data insights, ensuring you stay ahead of safety regulations. From small businesses to large enterprises, Knowella adapts to your needs and scales with your growth.
Take control of your workplace safety today. Get Started for FREE Today into a seamless, efficient process!
The primary goal of industrial ergonomics is to create a harmonious balance between workers, their tasks, and the tools they use. Key objectives include:
Discover the top 10 audit management software for 2025. Find the best tools to improve your audits today. Get your free demo now!
Looking for the best risk management software in 2025? See our list of top picks to keep your business secure. Get your free trial now.
Find software that helps you track cases fast. See our top 10 picks for 2025. Get the best tools to handle your investigations now.